Pressure treated lumber has been a staple in building and construction for decades, known for its durability and resistance to rot, decay, and insect attack. However, recent observations and user experiences suggest that the newer pressure-treated lumber doesn’t last as long as the old Chromated Copper Arsenate (CCA) treated lumber.
To understand why this is happening, it’s important to look into the changes in treatment processes and the source of the wood itself.
The Shift from CCA to Newer Treatment Methods
Historically, CCA was widely used for treating lumber, effectively preserving it for many years. However, due to environmental and health concerns associated with arsenic, the lumber industry shifted towards alternative preservatives. These newer treatments, while safer for consumer handling and the environment, often do not appear to protect the wood as well as CCA, potentially leading to reduced longevity.
What are the Newer Treatments?
The newer treatments used for pressure treated lumber, introduced as alternatives to Chromated Copper Arsenate (CCA), include several different chemicals designed to offer protection against rot, decay, and insect damage while being more environmentally friendly and safer for consumer use. Here are the most common types:
- Alkaline Copper Quaternary (ACQ): ACQ is a water-based wood preservative that prevents decay from fungi and insects. It’s a mixture of copper, which acts as the primary fungicide and insecticide, and a quaternary ammonium compound (quat) that provides additional protection against certain types of fungi and insects. ACQ-treated lumber is less toxic than CCA but can be more corrosive to metal fasteners and fittings.
- Copper Azole (CA): Similar to ACQ, Copper Azole is also a copper-based preservative. It contains copper and an organic azole compound, such as tebuconazole, as a co-biocide. This treatment is known for its effectiveness in protecting against termites and fungal decay. CA-treated wood is also less corrosive than ACQ-treated wood.
- Micronized Copper Azole (MCA): MCA is a variation of Copper Azole. It uses micronized copper particles in combination with a fungicide like tebuconazole. The micronized copper technology allows for a more uniform distribution of the copper particles, potentially improving the wood’s resistance to decay and insect damage.
Impact of Fast Growth Plantations
Another significant factor is the source of the lumber. Much of today’s pressure-treated wood comes from fast growth plantations, predominantly featuring trees with larger growth rings. This is a stark contrast to the old-growth Southern Yellow Pine, which had tighter growth rings. The difference in growth rings is not just a visual aspect but also a fundamental change in the wood’s properties.
Larger Growth Rings: A Drawback
The larger growth rings in plantation-grown trees indicate a quicker growth rate. While this is advantageous for producing lumber at a faster pace, it results in a lower density of the wood. Lower density wood tends to absorb and retain moisture more, making it more susceptible to rot and decay. Moreover, the treatment chemicals may not adhere as effectively to this less dense wood, leading to a potential decrease in the protective qualities of the pressure treatment.
Tight Growth Rings: The Strength of Old-Growth Timber
In contrast, the tight growth rings of old-growth Southern Yellow Pine meant a denser, more robust wood. The density of this wood not only provided a stronger material for construction but also allowed the CCA treatment to bind more effectively, ensuring long-lasting protection against environmental factors.
The combination of a shift from CCA to newer preservatives, and the use of wood from fast growth plantations, has culminated in pressure-treated lumber that does not appear to match the longevity of its predecessors.
While these changes have been driven by environmental and health considerations, they have inadvertently affected the durability and lifespan of the treated wood. This situation underscores the complex balance between sustainability, health concerns, and material performance in the construction industry.
50 Year Decking Boards Outlast the Deck Framing
The biggest issue we are seeing with some of our hardwood decking species like Ipe known to last up to 75 years is the deck boards are outliving the pressure treated framing.
We’ve received many calls from our customer that purchased Ipe wood from us 10-15 years ago that now have to rebuild their deck because the pressure treated framing is rotting. Their Ipe deck boards are still in great condition but the deck must be torn apart and rebuilt with new framing.
Many of the new composite decking and PVC deck boards are warrantied for 50 years as well but you will not find any pressure treated lumber that offers the same lifespan or a warranty that comes close to that.
New Building Practices Help Pressure Treated Lumber
In the recent years new building products such as joist tape and ledger tape have been introduced to help with an area where you most commonly see the newer pressure treated lumber rotting in the 10-15 year mark.
Joist tapes and ledger tapes get applied to the top of the joist and on the ledger to prevent water from getting trapped on the top of the joist and ledger.
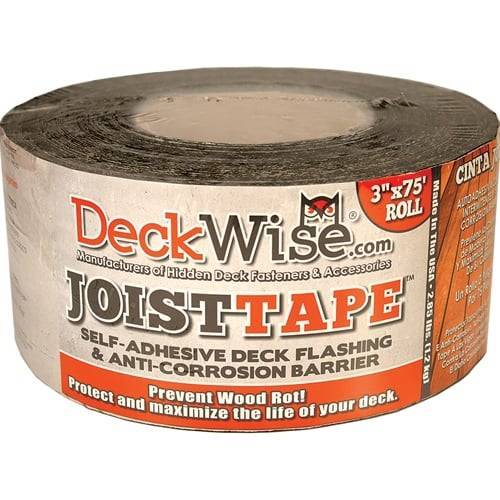
This area would see prolonged moisture as rain water get trapped in between the top of the joists and underneath the deck boards. Adding joist tape to the top and every joist and ledger tape across the entire deck ledger should significantly help with this issue.
Alternative Deck Framing Materials
There are newer alternative to pressure treated lumber that can be used for your deck framing. These include galvanized steel framing that is powder coated, aluminum deck framing, composite deck framing and LVL framing. While LVL is still a treated wood product, it got some significant benefits over traditional pressure treated and offers a nice warranty.
Stay tuned as we will be offering most if not all of these alternative deck framing materials in 2024.
Have pressure treated 4x4s since 1999 and have none rot at base where it contacts with soil.
Did a new wood fence at another place in the yard and six months later one fence post is rotted at base. Ridiculous
.
Your 4×4 posts from 1999 are the old arsenic treated version. The new treatment methods don’t last as long but yes 6 months is ridiculous. You need to take extra measures before placing them in the ground nowadays.