Wood is an incredible, natural material that has been used for thousands of years in countless applications, from furniture to homes and more. However, wood in its natural state can be prone to decay, fungi, and pests. To overcome these challenges, and enhance the durability of wood, a technique known as thermal modification has been developed. Let’s dive into what thermally modified wood is and how it’s made.
What is Thermally Modified Wood?
Thermally modified wood (TMW) is wood that has undergone a heat treatment process to improve its properties. The process changes the cell structure of the wood, reducing its equilibrium moisture content and making it more resistant to decay and insects. It does so without the use of chemicals, which means the end product is non-toxic and eco-friendly.
Benefits of Thermally Modified Wood:
- Enhanced Durability: TMW is significantly more durable than untreated wood, which makes it ideal for outdoor applications such as decking, siding, and furniture.
- Resistance to Pests: The thermal modification process makes the wood less appetizing to pests.
- Dimensional Stability: TMW is less prone to warping, swelling, and shrinking due to changes in moisture.
- Aesthetically Pleasing: The process can bring out a richer color in the wood, which many find appealing.
- Eco-friendly: Since the treatment doesn’t rely on chemicals, it’s a greener choice compared to chemically-treated wood.
How is Thermally Modified Wood Made?
The production of thermally modified wood can be broken down into several key steps:
- Preparation: Before the treatment, the wood is air or kiln-dried to a certain moisture content. This is crucial as it ensures uniform treatment and minimizes defects during the process.
- Heat Treatment: The actual modification takes place in a specialized kiln or chamber. Here, the wood is subjected to temperatures between 180°C (356°F) and 230°C (446°F). The precise temperature and duration depend on the wood species and the desired properties.
- Oxygen-Free Environment: To prevent combustion and control the modification process, the chamber is either vacuum-sealed or filled with an inert gas like nitrogen.
- Cooling: After the heat treatment, the wood is cooled down. This can be done naturally or with the aid of water.
- Conditioning: Once cooled, the wood is re-acclimatized to balance the internal stresses that might have developed during the heating process. This stage ensures the wood doesn’t warp or crack post-treatment.
- Final Drying: To bring the moisture content down to the desired level, the wood undergoes a final drying process. This ensures it’s ready for use or further finishing.
Products & Applications
Thermally modified wood can be used in an array of commercial and residential applications. Popular applications are in external environments where moisture and humidity would compromise a lesser-grade material.
- Decking: Arbor Wood decking is available in a range of species and profile options. Arbor Wood proves to be a more natural and durable alternative to chemically-preserved lumber.
- Siding: Arbor Wood siding is produced from domestically sourced and responsibly harvested wood. Arbor Wood is produced from a range of wood species, profile and finish options, including our take on traditional Japanese charred cladding.
- Ceiling: Arbor Wood ceiling/soffit is available in a range of species and profile options. Choose from T&G, V-Groove or Rainscreen.
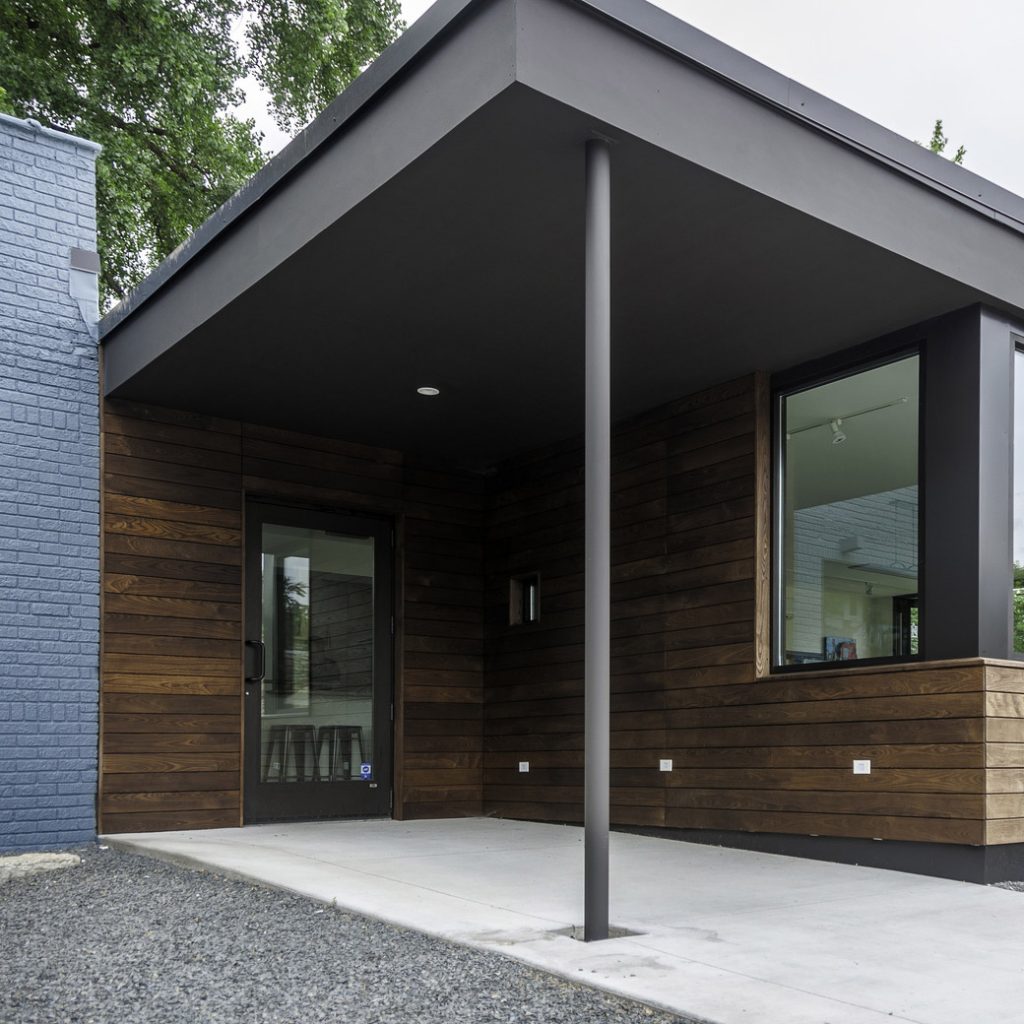
Final Thoughts:
Thermally modified wood offers a sustainable alternative to chemically treated wood, providing durability and aesthetic appeal. Its ability to resist decay and pests, combined with its dimensional stability, makes it a favorite choice for architects, builders, and homeowners alike. As we continue to look for eco-friendly and sustainable options in construction and design, thermally modified wood stands out as a front-runner in the industry.